Key maintenance of peripheral equipment for printing machines
Time:2025-07-02
Views:131
At present, there are two types of air pumps used in offset printing machines. One is the dry pump. One type is the oil pump.
1. Dry pumps supply air to printing machines by generating high-pressure gas flow through the rotation and sliding of graphite sheets. The general maintenance items for them are as follows:
1) Clean the pump‘s air inlet filter every week. Open the cover and remove the filter element. Clean with high-pressure air;
2) Clean the motor cooling fan and the air pump pressure regulating valve every month.
3) Every three months, oil the bearings. Use a grease gun to add grease of the specified brand to the grease nozzle.
4) Check the wear of the graphite sheets every six months. Remove the outer cover to take out the graphite sheets, measure their dimensions with a vernier caliper, and clean the entire air chamber.
5) A major overhaul should be carried out once a year (or after 2,500 hours of operation), during which the entire machine is disassembled for cleaning and inspection.
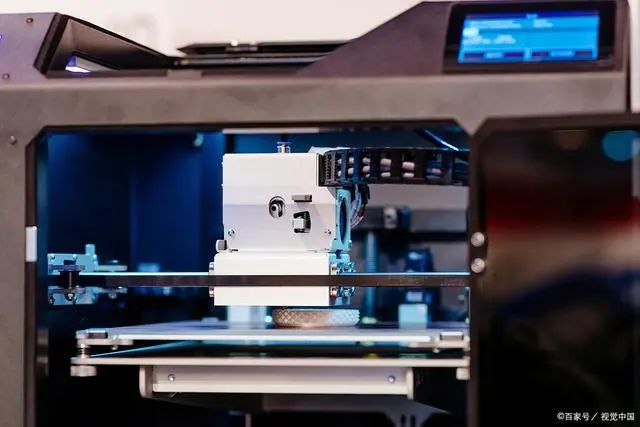
2. An oil pump is a type of pump that generates high-pressure gas flow by rotating and sliding stainless steel spring plates in the air chamber. Unlike dry pumps, oil pumps achieve cooling, filtration and lubrication through oil. The maintenance items are as follows:
1) Check the oil level every week to see if it needs to be refilled (make sure to turn off the power and let the oil flow back completely before observing).
2) Clean the air inlet filter every week. Open the cover plate, remove the filter element and clean it with high-pressure air.
3) Clean the motor cooling fan every month;
4) Change the oil every three months. Completely drain the oil from the oil pump‘s oil chamber, clean the oil chamber, and then add new oil. For new machines, the oil should be changed after two weeks (or 100 hours) of operation.
5) A major overhaul should be carried out once every year (or 2,500 hours) to check the wear condition of all major wearing parts.
.png)
In offset printing machines, the pressure control actions of the water-ink circuit, clutch pressure, etc. are achieved by the high-pressure gas supplied by the air compressor. The maintenance items are as follows:
1. Check the oil level of the compressor every day. It must not be lower than the red line mark.
2. Discharge the condensate water in the gas storage tank every day.
3. Clean the air inlet filter element every week and blow it with high-pressure air.
4. Check the tightness of the drive belt every month. After pressing the belt down with your finger, its springback range should be 10 to 15mm.
5. Clean the motor and heat sink every month.
6. Change the oil every three months and thoroughly clean the oil chamber. If it is a new machine, the oil needs to be changed after working for two weeks or 100 hours.
7. Replace the air inlet filter element every year.
8. Check the air pressure drop (leakage) every year of operation. The specific method is to turn off all gas supply facilities, let the air compressor rotate and inflate fully, and observe for 30 minutes. If the pressure drop exceeds 10%, check the seals of the compressor and replace the damaged ones.
9. Overhaul once every two years, disassemble for a comprehensive inspection and repair.
Under the control of the periodic paper collection by the paper collector, the high-pressure gas powder sprayer blows the powder in the powder sprayer above the paper collector and sprays it onto the surface of the printed matter through the powder sprayer holes. The maintenance items are as follows:
1. Clean the air pump filter element every week.
2. Clean the powder spraying control CAM every week. On the paper collection chain shaft, the sensing CAM may lose its periodic accuracy control due to excessive dust accumulation, so it needs to be cleaned regularly.
3. Clean the motor and cooling fan every month.
4. Unclog the powder spray pipe every month. If necessary, remove it and rinse it with high-pressure air or high-pressure water. Use a needle to unclog the small powder spray holes above the paper collector.
5. Clean the powder spraying container and mixer every month, pour out all the powder, and press the "TEXT" key on the powder spraying machine, which will blow out the residue in the container.
6. Check the wear of the pump graphite sheets every six months.
7. Carry out a major overhaul of the pressure air pump every year of operation.
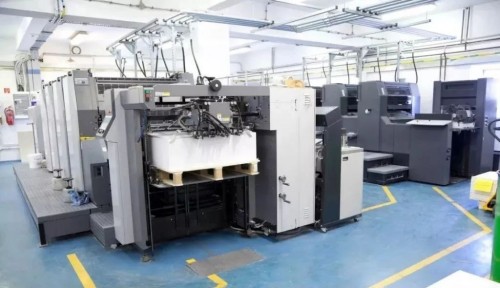
The high-pressure gas powder sprayer in the main electrical cabinet, under the control of the periodic paper collection by the paper collector, blows the powder in the powder sprayer above the paper collector and sprays it onto the surface of the printed matter through the powder sprayer holes. The maintenance items are as follows:
1. Clean the air pump filter element every week.
2. Clean the powder spraying control CAM every week. On the paper collection chain shaft, the sensing CAM may lose its periodic accuracy control due to excessive dust accumulation, so it needs to be cleaned regularly.
3. Clean the motor and cooling fan every month.
4. Unclog the powder spray pipe every month. If necessary, remove it and rinse it with high-pressure air or high-pressure water. Use a needle to unclog the small powder spray holes above the paper collector.
5. Clean the powder spraying container and mixer every month, pour out all the powder, and press the "TEXT" key on the powder spraying machine, which will blow out the residue in the container.
6. Check the wear of the pump graphite sheets every six months.
7. Carry out a major overhaul of the pressure air pump every year of operation.

The main oil tank of the current offset printing machines all adopt the rain lubrication method for lubrication. It is required that the main oil tank has a pump to pressurize the oil to each unit and then spray it onto the gears and other transmission parts for lubrication.
1. Check the oil level of the main fuel tank every week. It must not be lower than the red marking line. Since the oil pressed into each unit needs to return to the oil tank, it is generally necessary to turn off the power for 2 to 3 hours and then observe.
2. Check the working condition of the oil pump every month, and whether the filter screen on the suction head of the pump and the oil filter element are aged.
3. The filter element should be replaced every six months. For new machines, the filter element needs to be replaced after 300 hours of operation or one month. Method: Turn off the main power supply, place a container at the bottom, unscrew the filter body, take out the filter element, put in the new filter element, fill it with the same type of new engine oil, screw on the filter body, and then power on for a test run.
4. Change the oil once a year, thoroughly clean the oil tank, unclog the oil pipes and replace the suction pipe filter screen. The oil of a new machine should be changed once after 300 hours of operation or once a month, and then once a year thereafter.
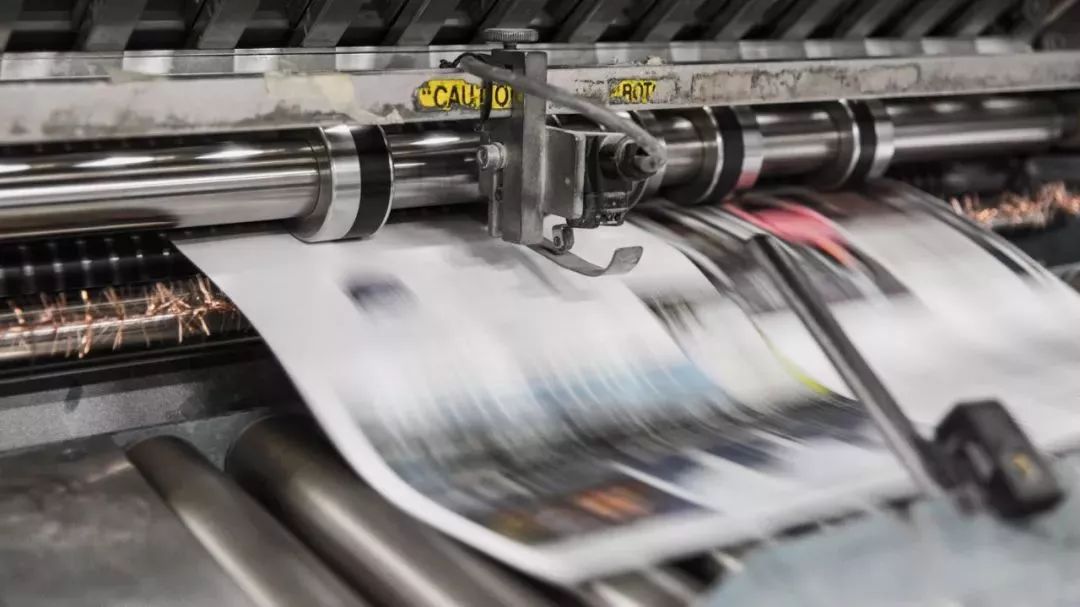
The paper collection chain is equipped with a periodic oiling device as it operates under high-speed and heavy-load conditions. The maintenance items are as follows:
1. Check the oil level every week and replenish it in time.
2. Check the oil circuit and unblock the oil pipes every month.
3. Thoroughly clean the oil pump every six months.